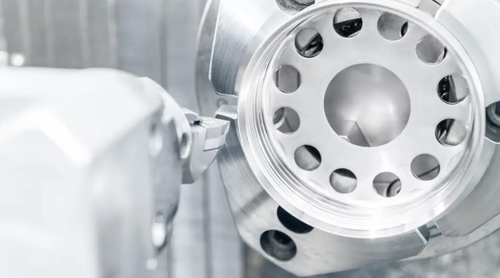
CNC turning is one of the key machining methods used in the industry to precisely shape cylindrical components. By utilizing Computer Numerical Control (CNC), this process is characterized by high accuracy, repeatability, and the ability to produce complex shapes efficiently. CNC turning is widely used in various industries, including automotive, aerospace, electronics, and machinery manufacturing.
What is CNC Turning?
CNC turning is a machining method in which a rotating workpiece is shaped by a cutting tool – a lathe tool. The entire process is computer-controlled, allowing for precise execution of even the most complex details. Machining can involve both external and internal turning, as well as additional operations such as grooving, threading, and drilling.
The CNC turning process consists of several key stages:
- CAD Design – Creating a 3D model of the part using specialized software.
- Generating CNC Code – Converting the design into a language understood by the CNC machine (G-code).
- Material Mounting – Securing the raw material in the lathe chuck.
- Machining – Cutting the metal using a properly selected lathe tool.
- Quality Control – Checking the dimensions and compliance of the part with the design.
Types of CNC Turning
CNC turning can be divided into several main categories depending on the machining method:
- Longitudinal Turning – Machining where the tool moves along the axis of the workpiece.
- Cross Turning – Cutting the material perpendicular to the axis of rotation.
- Profile Turning – Used to create complex shapes by replicating a given contour.
- Thread Cutting – Precision machining of internal and external threads.
- Taper Turning – Machining parts with a varying cross-section.
Applications of CNC Turning
CNC turning is widely used across various industries, including the production of:
- Automotive Components – Shafts, bushings, discs, and other mechanical parts.
- Aerospace Parts – Lightweight and durable components used in aircraft structures.
- Electronic Components – Precision enclosures and heat sinks.
- Machine Components – Drive shafts, screws, pins, and other high-precision parts.
Benefits of CNC Turning
The main advantages of using CNC turning include:
- High Precision – The ability to produce parts with very accurate dimensions and smooth surfaces.
- Repeatability – Ensuring identical quality for all components in serial production.
- Efficiency – Automation speeds up and optimizes the machining process.
- Flexibility – The ability to machine different materials, from metals to plastics.
- Minimal Material Waste – Process optimization reduces material loss.
How to Choose the Right CNC Machining Provider?
Selecting a professional CNC turning service provider is crucial for product quality and production efficiency. Key factors to consider include:
- Experience and References – Checking how long the company has been in the market and reviewing its past projects.
- Modern Machine Park – Advanced technologies and modern machines ensure top-quality machining.
- Service Range – It is essential that the company offers comprehensive services from design to quality control.
- Timeliness and Reliability – The ability to fulfill orders according to the schedule.
CNC turning is an advanced machining method that allows for the precise and efficient production of various-shaped components. Thanks to computer control, this process ensures high accuracy, repeatability, and efficiency. If you are looking for a reliable CNC service provider, Propart Sp. z o.o. offers comprehensive solutions in turning and other metal machining methods. Contact us for a customized quote and tailored solutions for your business!